- Homem
- Fuzzy Logic Control Trainer VPL FLCT
Fuzzy Logic Control Trainer VPL FLCT
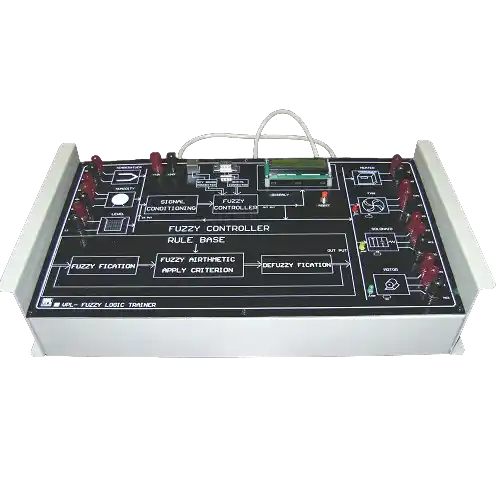
Fuzzy Logic Control Trainer VPL FLCT
The open design of the Fuzzy Logic Control Trainer (VPL-FLCT) allows the range of fuzzy logic and control experiments to be developed and extended as required to suit the specific interests of the user. In the case of fuzzy control, any external system with compatible inputs and outputs may be considered for control using fuzzy logic via the VPL-FLCT.
FEATURES of Fuzzy Logic Control Trainer (VPL-FLCT)
- Teaching aid to take the mystery out of fuzzy logic. May also be used by practising engineers for fuzzy logic familiarisation.
- Unique hardware module oriented for implementing fuzzy systems using fuzzy system elements.
- Students learn by defining fuzzy parameters membership function, Rules to get results.
- Compatible with Fruit-AX fuzzy system software allow user to define membership functions, graphs, setup rules, and facility to transfer the data on VPL-FLCT.
- Fuzzy systems complemented by links with Fruit-AX software to allow smooth progression to the more usual digital computer form.
- Allows rapid implementation and use of fuzzy systems.
- Manual contains full tutorial information for selfinstruction, from an introduction into the basic principles of fuzzy logic to performing practical real time fuzzy control experiments using control models or other compatible equipment.
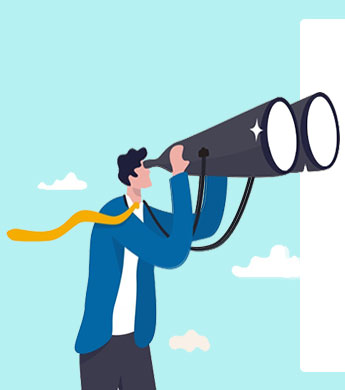
Tell us what are you "Looking for?"
Related Product
Related Product
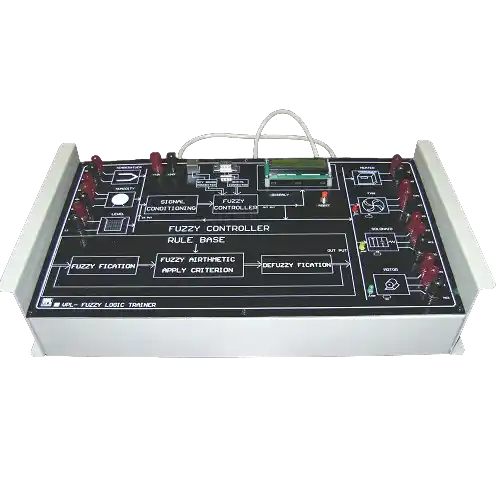
Distributed Control System Trainer VPL DCST
The Distributed Control System Trainer (VPL-DCST) is a type of automated system that is distributed to give instructions to different parts of the remote machine from Supervisory machine. VPL-DCST has two/three Remote stations and one Supervisory station. At each Remote station, we monitor analog inputs and outputs and take decision at the Supervisory station. SPECIFICATIONS of Distributed Control System Trainer (VPL-DCST) Hardware for Each Remote Station: Analog Input Module Resolution : 16bit Input Channel : 8 differential Sampling rate : 10Hz Voltage Input : +/-150mV, +/-500mV, +/-1V, +/-5V,+/-10V Current input : +/-20mA Isolation Voltage : 3000V Dual Watchdog Timer Over Voltage Protection : +/-35V Digital Output Module Output Channels : 8 Isolation with common power Isolation Voltage : 3750Vrms Load Voltage : Max +30V Max Load Current : 375mA Input Channels : 4 Digital Level 0 : 1V Max Digital Level 1 : 4 to 30 V Input Impedance : 3k ohms Power Input : +10 to +30 VDC Power Consumption : 1.7W RS-232 to RS-485 Converter RS-232 Interfaces are full-duplex and require just data signals Signals : TX, RX Baud Rates : Std Windows rates upto 115.2 kbaud Data Bits : 7 or 8 bits Parity : None, odd or even Stop bits : 1 or 2 Flow Cntrol : None RS-485 Interface is half-duplex and includes self tuner and network protection Signals : TX/RX pair Baud Rates : Std Windows rates upto 115.2 kbaud. Data Bits : 7 or 8 bits Parity None : odd, or even Stop bits : 1 or 2 Distance : 1200 M
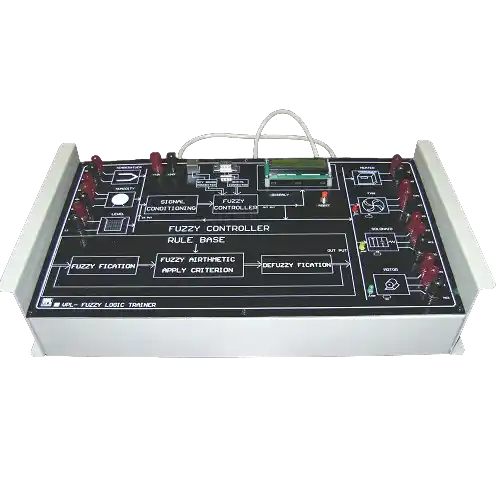
Electro Hydraulic Trainer With VPL PLC VPL HTPLC
The system is designed for the training experiments of hydraulic technology in higher education and vocational education field. It covers the most knowledge of hydraulic techniques. It can be used as a synthesized test-bed for mechanical, electrical and hydraulic integration. The kit is capable of being used to demonstrate the design, construction and application of electro-hydraulic components and circuits. SPECIFICATIONS Trolley with frame – No of wheels 04, two fixed & two swivel type. Hydraulic power pack – operating pressure =40 bar, Flow rate =3LPM, tank capacity =17 liters, Suitable pump & electric motor coupled with bell housing and mounted externally over the tank. Pressure gauge (glycerin filled) 3 nos. of suitable range to measure the pressure. One way Flow control valve – 01 no Double acting cylinder – 02 nos. Double actuating solenoid controlled valve – 01 no. 4/3 way hand lever valve – 01 no Tee connectors Operation and maintenance manual VPL Programmable Logic Controller
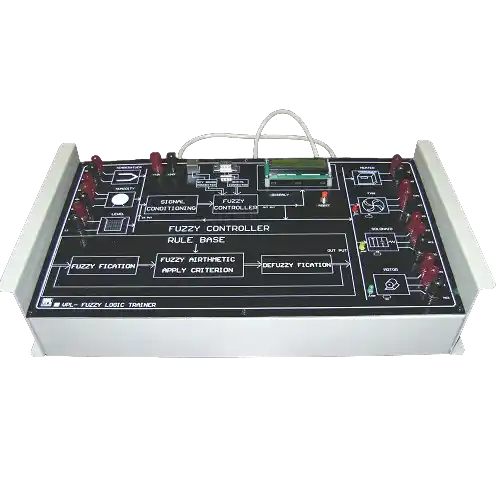
Finger Print Trainer VPL FP I
The VPL Finger Print Trainer (VPL-FP-I ) is designed for the training finger print recognition and verification. It can store up to 468 fingerprint templates on board flash which can be extended upto 1000 templets. Its core is ARM7TDMI32 bit RISC core with 8k byte cache. SALIENT FEATURES of Finger Print Trainer (VPL-FP-I) Fingerprint registration and verification. Up to 468 fingerprint templates can be stored on board flash. 122×32 dotmatrix LCD with background light support. Two RS232 ports and one RS485 port for connecting to PC. 7 expandable connectors for connecting to external circuits. 4K bytes EEPROM for saving any general data. 16 keys pinpad for user input. Real time clock display. Power can be retrieved from the PS/2 port or external adapter. Built in demo application firmware. Built in debug monitor for manual operation of the board. 3 options of ‘USER’, ‘VIP’ & ‘ADMIN’ during registration. User can enter time and date through keypad. Can connect external modules like Smart Card Reader etc. TECHNICAL SPECIFICATIONS Power supply: 220V/AC @ 50 Hz ±10% Current input: Typically 250mA (550mA working current) Core: ARM7TDMI 32 bit RISC core with 8k byte cache Memory: 512K byte Flash, 2M byte SDRAM, 4K byte EEPROM Communication: RS232C Connectors: 8 pin GPIO, 12 keyboard scan line, SPI, Mono LCD, 2 external interrupt, JTAG, IrDA, MultiMedia card, UART, Buzzer, Smartcard Storage: Up to 468 fingerprint template expandable upto 1000 template
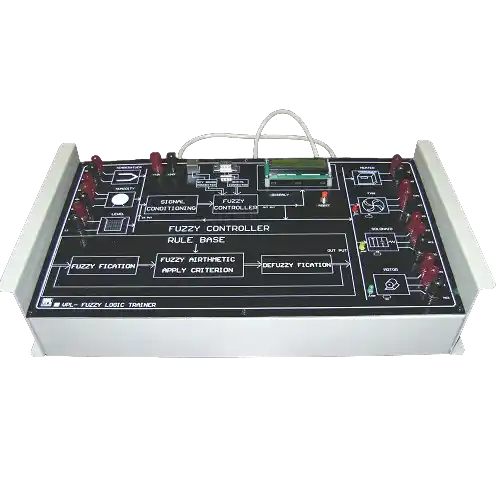
PID Controller Trainer VPL CL PID
PID Controller Trainer (VPL-CL-PID) This set up is designed to study performance of analog PID Controller with simulated process. The board has built in signal source, building blocks for simulated process and PID Controller with built in regulated dc supply to operate the system. The PID Controller has three adjustable parameters, as P, I, D each has 10 turn potentiometers with dial knobs which are subdivided for .02 resolution. Three sockets are provided to add or out any of desired control P, I or D. at input of PID controller an adder is provided which sums the reference and feedback signals. The input and output of PID control has no phase shift. The PID Controller has three adjustable parameters, as P, I, D each has 10 turn potentiometers with dial knobs which are subdivided for .02 resolution. Three sockets are provided to add or out any of desired control P, I or D. at input of PID controller an adder is provided which sums the reference and feedback signals. The input and output of PID control has no phase shift.
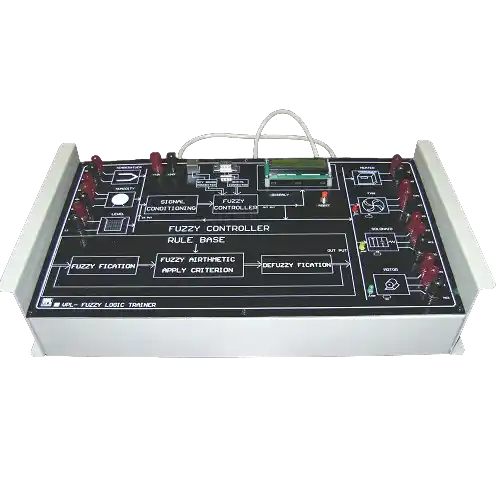
PLC Demonstration Trainer VPL PLCT
PLC Demonstration Trainer (VPL-PLCT) PLC Trainer has been designed in a different way than conventional PLC suitable to impart training and use of PLC in Process Industry for students at all levels with 16 Input Switches and 16 Output LEDs to simulate the Ladder Program, assembler to generate ladder programs, descriptive user manual with number of examples including description & fundamentals of PLC, number of Experimental Panels to be connected to the PLC for practical demonstration of PLC uses (optional)
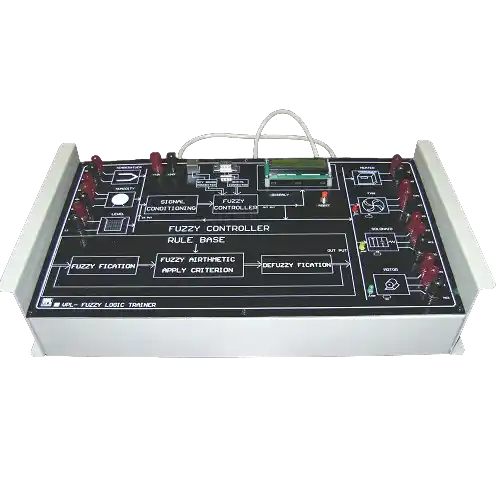
PLC Trainer Siemens with HMI VPL PLCTS HMI
PLC Trainer (Siemens) with HMI (VPL-PLCTS-HMI) Siemens Simatic PLC Trainer can control a wide variety of devices to support your automation needs. The Siemens PLC monitors inputs and changes outputs as controlled by the user program, which can include Boolean logic, Counting, Timing, Complex math operations and Communication with other intelligent devices. The compact design, flexible configuration and powerful instruction set combine to make the PLC a perfect solution for controlling a wide variety of applications.
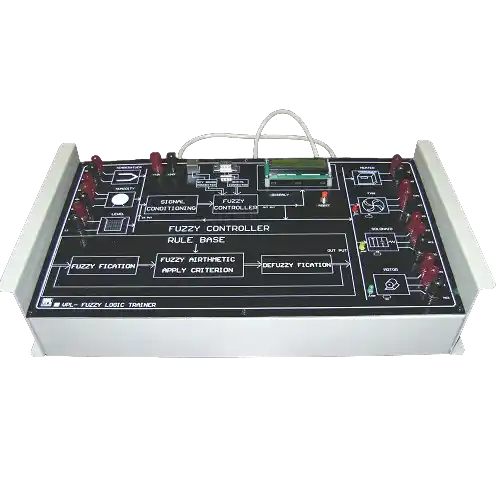
PLC Trainer Kit For Allen Bradley VPL PLCT AB
PLC Trainer Kit For Allen Bradley (VPL-PLCT-AB) The micrologic 1000 PLC Trainer can control a wide variety of devices to support your automation needs. The Micrologic PLC monitors inputs and changes output as controlled by user program which can include Boolean Logic, Counting, Timer, Complex math operations. The compact design, flexible configuration and powerful instruction set combine to make the PLC a perfect solution for controlling a wide variety of applications.
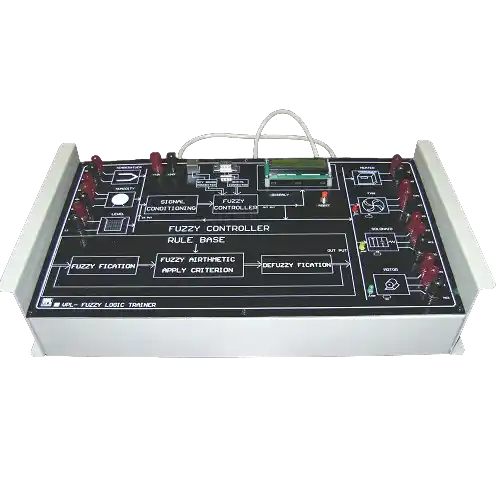
PLC Trainer Siemens VPL PLCT S313
PLC Trainer Siemens (VPL-PLCT-S313) Siemens Simatic PLC Trainer can control a wide variety of devices to support your automation needs. The Siemens PLC monitors inputs and changes outputs as controlled by the user program, which can include Boolean logic, Counting, Timing, Complex math operations and Communication with other intelligent devices. The compact design, flexible configuration and powerful instruction set combine to make the PLC a perfect solution for controlling a wide variety of applications.
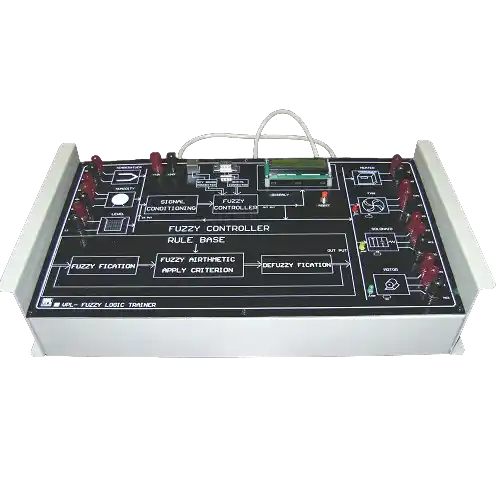
PLC Trainer with Demonstrator VPL PLCT S200
PLC Trainer with Demonstrator (VPL-PLCT-S200) The Siemens PLC monitors inputs and changes outputs as controlled by the user program, which can include Boolean logic, Counting, Timing, Complex math operations and Communication with other intelligent devices. The compact design, flexible configuration and powerful instruction set combine to make the PLC a perfect solution for controlling a wide variety of applications.
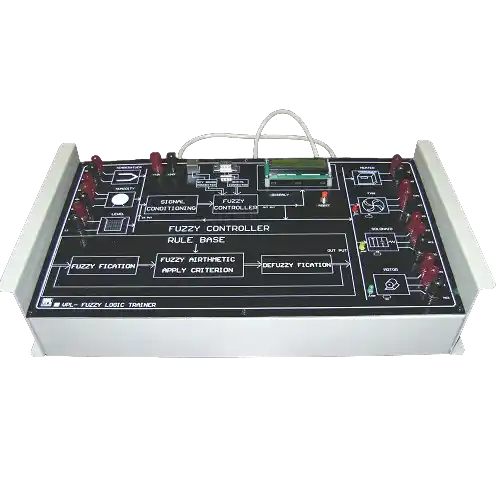
Pneumatic Trainer With Electronic Controller VPL PTEC
Pneumatic Trainer With Electronic Controller (VPL-PTEC) The system is designed for the training experiments of pneumatic technology in higher education and vocational education field. It covers the most knowledge of pneumatic techniques. It can be used as a synthesized test-bed for mechanical, electrical and pneumatic integration. The kit is capable of being used to demonstrate the design, construction and application of electro-pneumatic components and circuits.
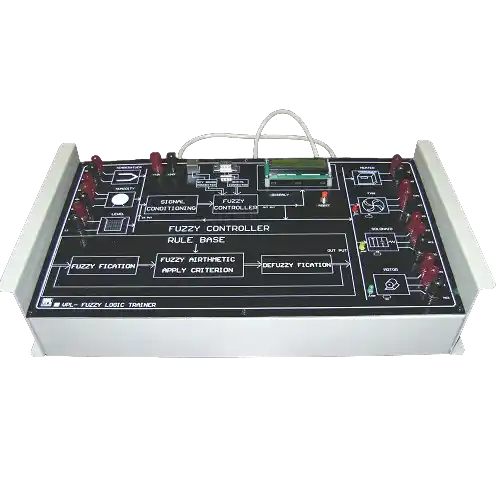
Smart Card Trainer VPL SC 01
Smart Card Trainer (VPL-SC-01) This VPL Smart Card Trainer (VPL-SC-01) is hels to understand students the technology behind modern days smart cards. They get familiar with technology behind contact less transmission of data wand supply energy (without use of battery), data security by mutual three pass authentication, data encryption on RF channel etc. Contactless transmission of data and supply energy (no battery needed). Operating distance: Up to 100mm (depending on antenna). Operating frequency: 13.56 MHz Fast data transfer: 106 kbit/s High data integrity: 16 Bit CRC, parity, bit coding, bit counting True anticollision Typical ticketing transaction: <100 ms (including backup management)
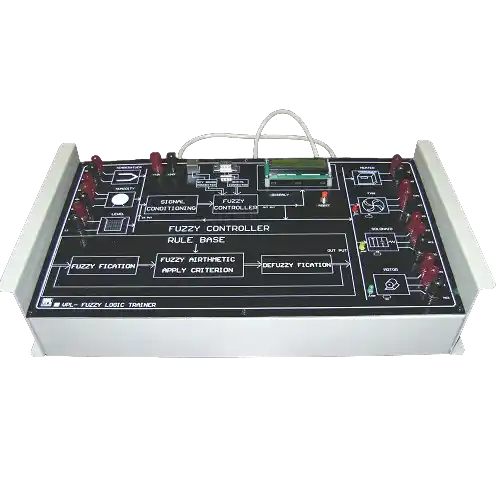
Synchro Transmitter Receiver Trainer VPL CL STR
Synchro Transmitter Receiver Trainer (VPL-CL-STR) A Synchro Transmitter Receiver (STR) Trainer is an electromagnetic transducer commonly used to convert an angular position of a shaft into an electric signal. It is usually called a synchro transmitter. Its construction is similar to that of a three phase alternator. It consists of Sator, Rotor, Synchro Transmitter and Synchro Receiver. A Synchro Transmitter Receiver (STR) Trainer is an electromagnetic transducer commonly used to convert an angular position of a shaft into an electric signal. Its construction is similar to that of a three phase alternator. The stator (stationary member) is of laminated silicon steel and is slotted to accommodate a balanced three phase winding which is usually of concentric coil type (three identical coils are placed in the stator with their axis 120 degrees apart) and is Y connected. The rotor is a dumb bell construction and wound with a concentric coil. The system set up is made up of synchro transmitter and synchro receiver on a single rigid base provided with suitable switches and anodised angular plates. The system also contains a step down transformer for providing excitation to the rotors. Suitable test points for rotor (R1 and R2) and stator (S1, S2 and S3) for both Tx and Rx are provided.
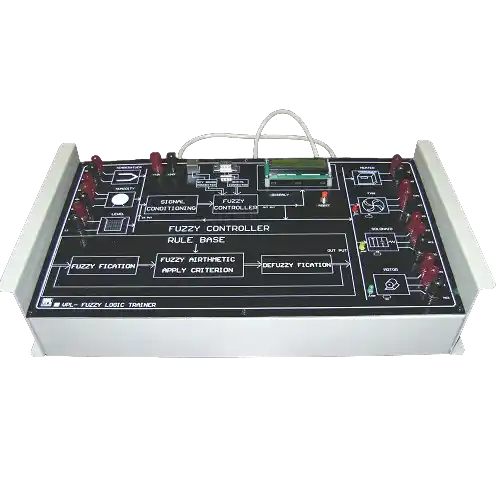
Temperature System Simulator VPL CL TSS
Temperature System Simulator (VPL-CL-TSS) This set up is designed to study performance of analog PID controller with model process as temperature control system. The set up has built in signal source as reference, digital voltmeter as temperature indicator, PID controller with separate controls and a model process with built in regulated DC supply to operate the system. The controller parameters are controlled by PID controls in which I control can be out of circuit by mean ‘I ON’ control switch. The D control is made out by mean of keeping D control to minimum or fully counter – clockwise direction. The set point temperature is adjusted by ‘SET POINT’ control while the reference temperature is read by digital display keeping TEMP switch to set point direction. The heater may be cut-off regardless of any setting by mean of ‘HEATER ON’ switch. A fan is included in the oven which is used to bring temperature below when the heater is off. The similar one is used to add disturbance when the set up is running under PID control mode.